In a hot runner system, the hot runner temperature controller is responsible for precisely controlling the melt temperature to ensure the quality of injection-molded products. The stability of its temperature control directly affects the final product's quality. Below, we will detail the working principle of the hot runner temperature controller and its key components.
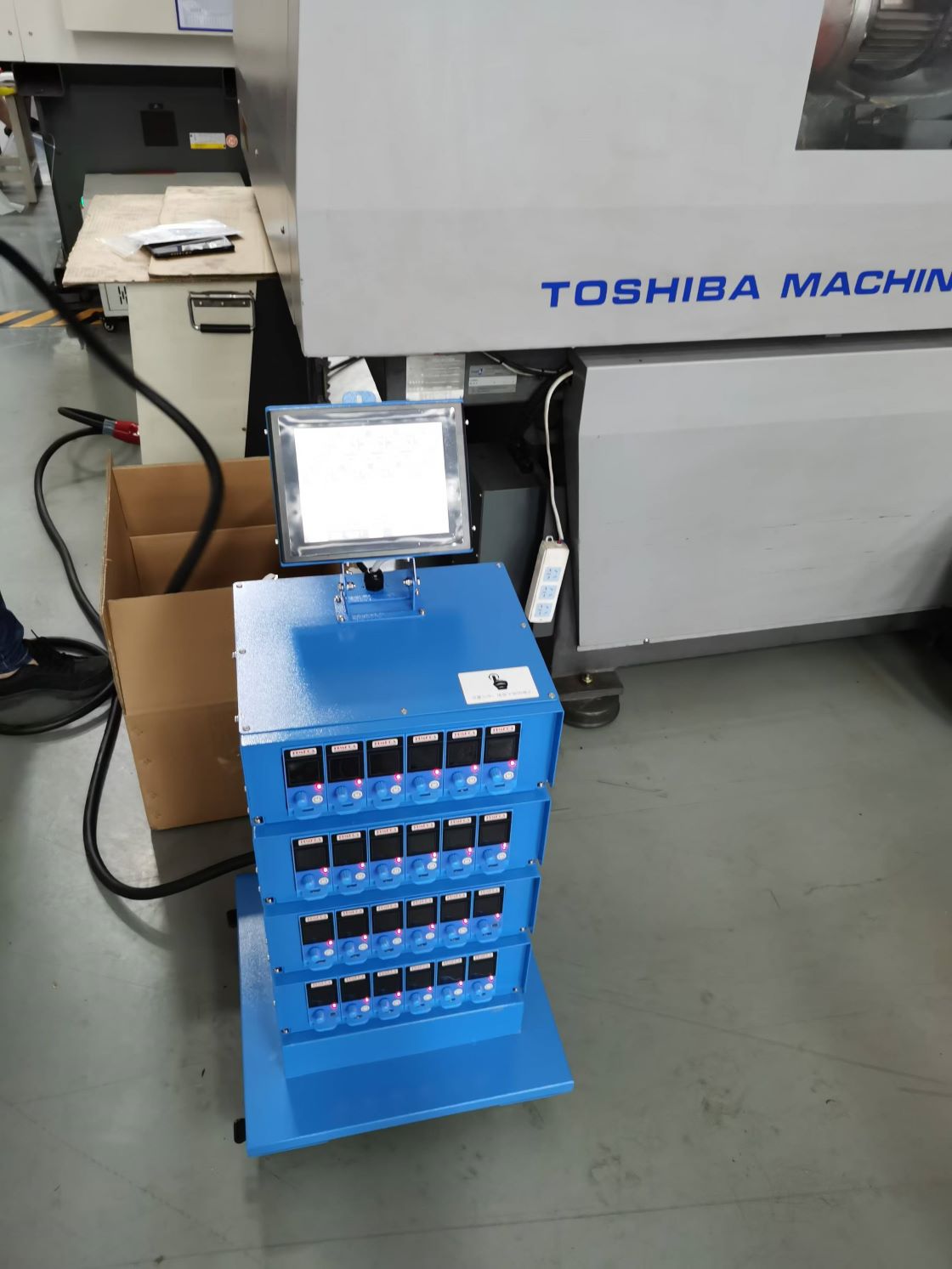
Key Components
1. Heater
Hot runner systems typically use electric heaters, which offer advantages such as small size, fast heating speed, and lower cost compared to oil heaters. Common electric heaters operate at voltages between 200-240V, while some hot runner companies also use low-voltage heaters.
2. Temperature Sensor
Temperature sensors are crucial for ensuring accurate temperature measurement. Common types include resistance temperature detectors (RTDs) and thermocouples. Due to the limited temperature range of RTDs (usually not exceeding 250°C), hot runner systems generally prefer thermocouples, which have a wider temperature range.
3. Temperature Controller
Given the high temperature control requirements and harsh working environment of hot runner systems, specialized hot runner temperature controllers are used instead of conventional temperature control instruments. For ease of replacement and maintenance, these controllers often feature a plug-in design, known as hot runner temperature control cards. These control cards are powerful and easy to maintain.
Work Process
The work process of the hot runner temperature controller is as follows:
- Signal Acquisition: The hot runner temperature control card periodically collects temperature signals from the thermocouple sensor and calculates the current actual temperature of the hot runner system.
- Temperature Comparison: The CPU compares the actual temperature with the preset target temperature, performs control calculations, and determines the power required for the heater.
- Power Adjustment: By adjusting the power output of the heater, the system achieves precise temperature control, ensuring that the temperature remains within the set range.
Through this method, the hot runner temperature controller continuously monitors and regulates the temperature, maintaining the melt temperature in the optimal state during the injection molding process. This results in improved production efficiency and product quality.